PRESS RELEASE
The Institute of Technical Physics and Materials Sciences of the Centre for Energy Research (EK MFA) along with BHE Bonn Hungary Electronics Ltd. have developed battery and wireless sensor networks which can be deployed in extreme environments. The sensor nodes scavenge energy from thermal and mechanical vibration sources from the ambient and communicate by a newly developed wireless RF protocol. These networks can be used in various real-life applications for health monitoring of civil infrastructures, real time monitoring of bicycle traffic and vehicle control systems.
Sensors, in continuously growing numbers, provide information in various fields of life, such as smart factories, transportation infrastructures, and agriculture. These devices have to be positioned often in hardly accessible places where the wiring of the sensor or, in case of wireless sensor, the battery replacement is either not feasible or expensive. In those cases, energy harvesting provides a viable solution. However, the exploitable sources are usually of low level, moreover their intensities fluctuate strongly in time and in place. The aim of project was to develop smart autonomous systems which can adopt to the stochastic environment and are extremely power efficient.
The vibrational energy harvesters and senor chips have been developed in the clean rooms of EK MFA who has a more-than-20-years’ experience in the field of micromechanical systems (MEMS) (www.nems.hu). The second stakeholder of the consortium, BHE Bonn Hungary Electronics Ltd., as a fully Hungarian own high-tech company provided the required know-how to develop energy efficient RF transmitters and sufficiently fast and sensitive receivers. Members conducted basic and applied research as well as proof-of-concept (PoC) developments in the project as described below.
The aim of the basic research was to investigate and realize novel type of vibrational energy harvesters and frequency selective accelerometers having multiple electrodes. Conventional non-resonant accelerometers provide uniform response in a broad frequency range; however, their sensitivity is often insufficient and require power supply. The researchers of EK MFA proposed a double side clamped Fermat spiral having segmented top electrode. The operation principle of the device, fabricated in a 30-step standard semiconductor process, was verified by a frequency swept electromagnetic shaker. In order to maximize the piezoelectric signals of the sensors, CMOS compatible nitride alloy layers, such as ScAlN was also investigated in the project. By optimizing the technological conditions, ScAlN thin films showed a 5-times increase in the longitudinal piezoelectric coefficient compared to the conventional binary AlN (~6.0 pC/N) on Si substrate. At similar deposition parameters this value was found to be even higher for Ni substrate (~10.0 pC/N), which bodes well for several applications where the high fracture strength is concerned.
Experts at BHE has developed two types of broad-range antennas (0.7-18 GHz) which are capable to extract energy from conventional RF sources, such as GSM, UMTS, LTE, digital TV systems or even 5G network.
Highlighted proof-of-concept systems:
Self-powered vibration diagnostic sensor (VibAn): The aim of the vibration diagnostic is the health monitoring of various machines having rotating parts. These tests are usually done occasionally upon insufficient machine operation. However, there is an increasing demand for failure prevention by posteriorly placed real-time monitoring systems. The wireless sensor node, developed by the project partners, can detect vibrations in all x, y, and z directions in the frequency range of 10 Hz-2 kHz and has a low average power consumption (~1 mW). The energy harvesting function was demonstrated by both vibrational and thermoelectric generators. The recorded sensor data are sent via a novel, low power RF protocol developed by the consortium members and their subcontractor (Ante Ltd., www.ante.hu/en/). The system consists of three units: i) a low-power transmitter circuit for the sensor node, which is capable of sub-microsecond RF pulse generation at the ISM RF band of 2.4 GHz; ii) a receiver enabling to record time intervals with a resolution of 40 ns from up to 32 sensor nodes and submit each data into the cloud via IP-based protocol; and iii) data acquisition and decoding software running on the remote server.
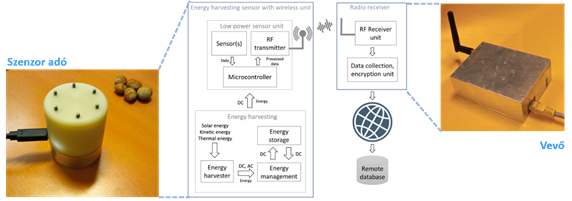
Integrated tire deformation sensor (TireForce)
Advanced vehicle control systems, especially self-driving vehicles, are gathering more and more information on the go to increase efficiency, reduce emissions, and increase safety. A set of sensors are installed today in the engine and placed in different locations of the car to monitor the vehicle’s movement and the environment. However, the interaction between the tire and road surface is not monitored yet. In the proposed concept, it is done through tracking of the tire deformation by an in-house developed 3D MEMS sensor which is mounted on the inner sidewall of the vehicle tire. The integrated tire sensor can provide valuable information about the surface condition of the road and predict tire slipping in advance. In cooperation with the Institute for Computer Science and Control (SzTAKI) EK MFA team has carried out several dynamic tests on ZalaZone (https://zalazone.hu/) and kick-plate tracks. A neural network with 3 hidden layers and altogether 114 neurons was used to teach the tire sensor with the assistance of on-board sensors of the car (Nissan Leaf). After the teaching process the predicted output values showed excellent agreement with several dynamical parameters, such as yaw rate, and transversal/longitudinal accelerations, which proves its potential in next generation vehicle control systems.
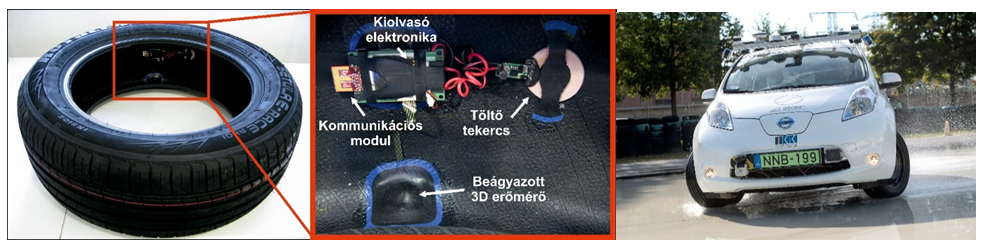
Bicycle traffic monitoring (LogLine): The portable sensor-line was developed on the demand of traffic experts to record the number, the crossover position, the speed, the moving direction, and wheelbase of the passing bicycles. The recorded data are transmitted by a solar-cell powered data collector unit using LoRaWAN narrow-band RF protocol. So far almost 270,000 cyclers have been counted by the LogLine sensor all around Budapest (https://logline.hu/).
Further Information:
EK MFA Nanosensors Lab: http://www.nems.hu
BHE Bonn Hungary Electronics Ltd: http://www.bhe-mw.eu/
Contact:
János Volk, principal investigator, www.nems.hu
EK MFA, 1121 Budapest Konkoly Thege Miklós út 29-33.
volk@mfa.kfki.hu , +36 1 392 2222/3474